6 Sigma and DMAIC – The Improve Phase is made easy by the great work done in the previous phases especially analyze.
Once you have an idea of the relationship between cause and effect this phase becomes pretty much about identifying what the appropriate countermeasure or change that is required to provide the desired outcome and then implementing.
Creating a project plan is going to make life a lot easier and agreement on how to implement including the – who, what, why, where and when.
Implementing Improvements
Utilizing a Gantt chart to help organize and track activities including sequence of those activities and any inter-dependencies will provide the high level visibility required to determine optimum results.
In addition to creating a Gantt, key information including start and end dates, required resources and budgets need to be monitored and tracked through out to ensure resources and effort and project quality are aligned.
Failure Mode and Effect (FMEA) is often used to enable the team involved to identify potential impact of proposed changes to a process. During an FMEA process you can rank risks through the risk priority numbering system built in and from this identify potential countermeasures and therefore manage the risks as they are identified.
When a change is being made its good practice to make that change on a small scale, check the results are in line with expectations and then if they are roll-out in a phased way as to not disrupt operations.
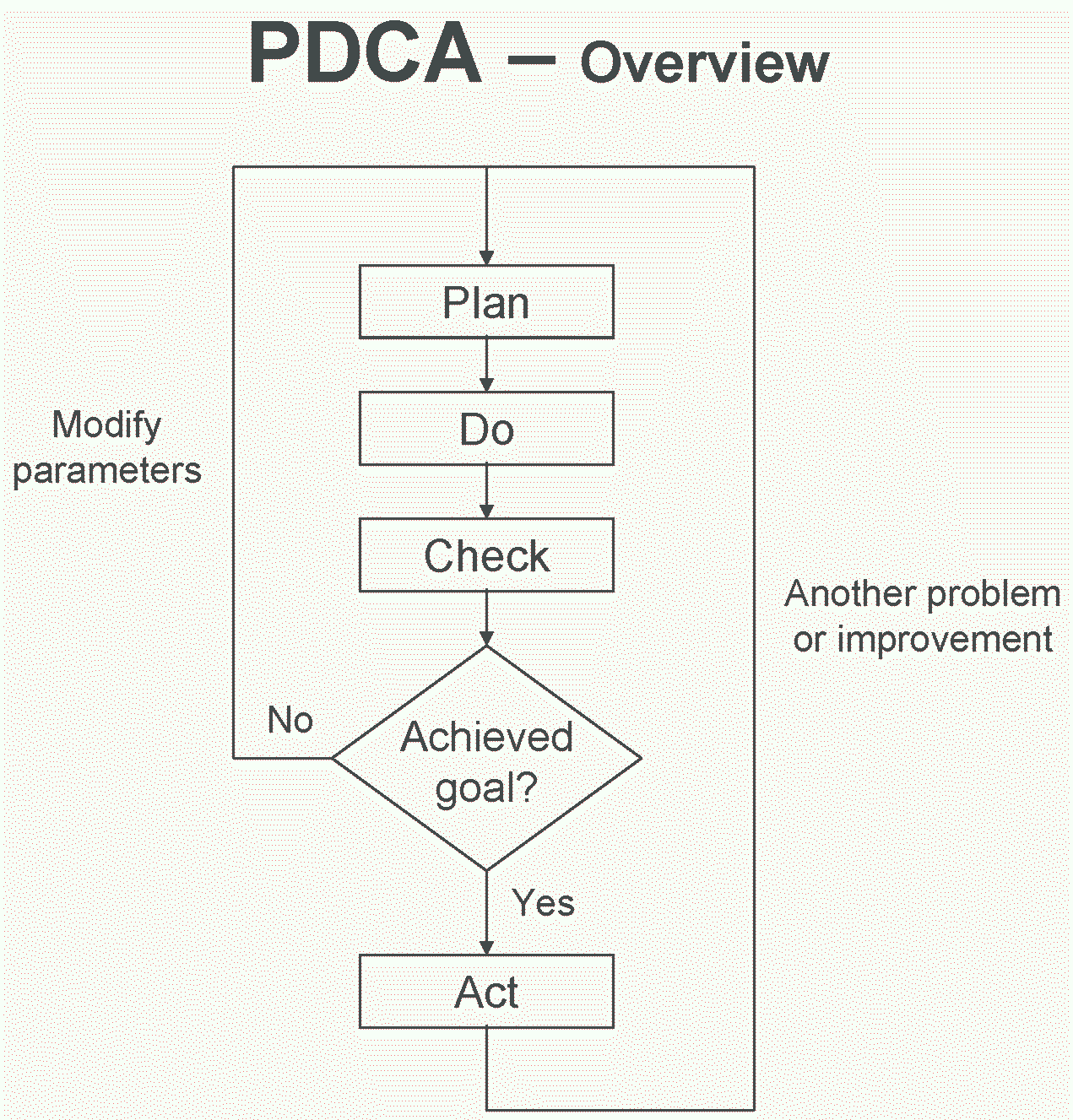
6 Sigma and DMAIC – The Improve Phase
Quality Function Deployment
QFD enables company management to focus on customer needs before a product is produced. It has the benefit of enabling design teams to get the product right for the customer the first time, thus reducing the need for expensive redesigning.
QFD:
• Improves communication and teamwork in the value chain
• Provides a better understanding of product objectives
• Makes all key information available for use in the design of products and processes
• Focuses on information about customer satisfaction and dissatisfaction
• Can simulate the effect of new design ideas
• Reduces time for new product development
• Improves competitive advantage with reduced time-to-market
HOQ is the first step in the QFD process. It helps an organization understand customer needs by providing a set of matrices to relate the VoC to:
• Product technical requirements
• Component requirements
• Process control plans
• Manufacturing operations
This process is called a house because of its appearance. Evans and Lindsay (2005) list the six basic steps of building an HOQ:
1. Identify customer requirements.
2. Identify technical requirements and the relationships between them.
3. Relate the customer requirements to the technical requirements.
4. Evaluate competing products or services.
5. Evaluate technical requirements and develop targets.
6. Determine which technical requirements to deploy in the remainder of the production process.
In my next Article we look at the Control phase and explore tools used and the approach taken
We really hope you have found this article of value and that it has inspired you to learn more about 6 Sigma and DMAIC – The Improve Phase, just remember the hardest part of any journey is getting started but once begun you will learn it’s an enjoyable and rewarding experience that can improve your organization’s culture and performance in a very positive way.